Researchers of Karlsruhe Institute of Technology (KIT) have developed and successfully tested an innovative concept for simultaneous coating and drying of two-layered electrodes. Drying times can be reduced to less than 20 seconds, which corresponds to half down to one third of the usual production time, without capacity losses of the battery. With the help of the concept, lithium-ion batteries can be produced more rapidly and at lower cost. The results are reported in Energy Technology (DOI: 10.1002/ente.202100367).
Electric vehicles will be of central importance to future mobility. This will result in a constantly growing demand for powerful and inexpensive batteries. In lithium-ion batteries, electrode layers are of decisive importance, as these active materials store the energy. However, coating and subsequent drying of electrodes cause most of the battery production costs. A big cost reduction potential lies in process engineering. Researchers of the Thin Film Technology (TFT) Group headed by Professor Wilhelm Schabel and Dr. Philip Scharfer have been conducting research in this area for years now. They already succeeded in considerably increasing coating speed and developed an innovative drying process. Now, the group has combined coating and drying in a simultaneous concept. The results are reported in Energy Technology, the main author being Jana Kumberg, doctoral researcher at KIT. TFT develops technologies for electrode production within CELEST – Center for Electrochemical Energy Storage Ulm & Karlsruhe, one of the biggest battery research platforms worldwide.
Cheaper Production
“Our work shows that in principle, we manage all process steps needed to produce batteries more rapidly and, hence, at lower cost in future without affecting quality,” Schabel explains. At usual electrode drying times of up to one minute and production speeds of one hundred meters per minute and more, long drying lines are needed. In case of electrodes with a high coating weight, this is hardly feasible and very expensive. The new concept is based on the idea of using different active materials for the layers and applying them simultaneously. One layer is responsible for adhesion, another for specific capacity. This layer structure enables manufacture at a very high drying rate, drying times are shortened to one third.
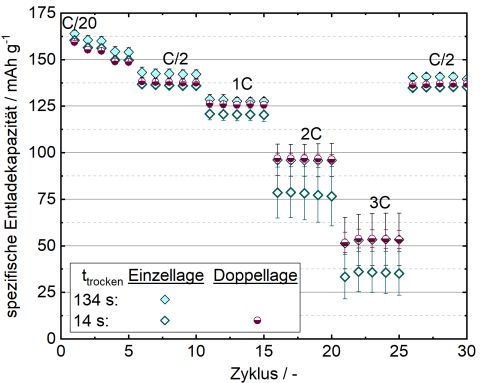
slowly dried single layer do not differ in capacity. As expected, the rapidly dried
single layer exhibits considerable losses. (Figure: Jana Kumberg, KIT)
Specific Distribution of Properties in the Electrode Layers
In spite of the reduced drying time, no capacity losses occur. The range of the battery remains the same, also in case of so-called 3C cycles i.e. rapid charging times of twenty minutes. Within their study, the scientists applied different active materials over the thickness of the anode, as a result of which different properties were distributed specifically in the electrode layers. In this way, electrodes can be customized and have better mechanical and electrochemical properties. “We have achieved first promising results,” Schabel says. “Now, we will work on industrial implementation.” At the moment, the group is working on ways to transfer the simultaneous concept to the industrial scale. For this purpose, it tests purely convective drying with high-performance nozzles and laser drying modules.
Studies are funded with more than EUR 5 million by the Federal Ministry of Education and Research (BMBF) within different research cluster projects. “Our research demonstrates that it may be possible in principle to increase battery production speed by two hundred to three hundred percent,” Schabel says. Now, the results are being transferred to other materials and used to optimize electrodes of sodium-ion batteries within the POLiS – Post Lithium Storage Cluster of Excellence.
Original Publication (Open Access):
Jana Kumberg, Werner Bauer, Joyce Schmatz, Ralf Diehm, Max Tönsmann, Marcus Müller, Kevin Ly, Philip Scharfer, and Wilhelm Schabel: Reduced Drying Time of Anodes for Lithium-Ion Batteries through Simultaneous Multilayer Coating. Energy Technology, 2021. DOI: 10.1002/ente.202100367
https://onlinelibrary.wiley.com/doi/10.1002/ente.202100367
More information on CELEST: https://www.celest.de/en/
More about the KIT Energy Center: https://www.energy.kit.edu/
Being “The Research University in the Helmholtz Association”, KIT creates and imparts knowledge for the society and the environment. It is the objective to make significant contributions to the global challenges in the fields of energy, mobility, and information. For this, about 10,000 employees cooperate in a broad range of disciplines in natural sciences, engineering sciences, economics, and the humanities and social sciences. KIT prepares its 22,800 students for responsible tasks in society, industry, and science by offering research-based study programs. Innovation efforts at KIT build a bridge between important scientific findings and their application for the benefit of society, economic prosperity, and the preservation of our natural basis of life. KIT is one of the German universities of excellence.