Researchers at the Karlsruhe Institute of Technology (KIT) have developed a system for fully automated monitoring of ball screw drives in machine tools. A camera integrated directly into the nut of the drive generates images that an artificial intelligence continuously monitors for signs of wear, helping to reduce machine downtime.
In mechanical engineering, maintaining and replacing defective components timely in machine tools is an important part of the manufacturing process. In the case of ball screw drives, such as those used in lathes to precisely guide the production of cylindrical components, wear has until now been determined manually.
“Maintenance is therefore associated with installation work, which means the machine comes to a standstill,” says Professor Jürgen Fleischer from the Institute for Production Technology (wbk) at the Karlsruhe Institute of Technology (KIT). “Our approach, on the other hand, integrates an intelligent camera system directly into the drive, which enables a user to continuously monitor the spindle status. If there is a need for action, the system informs the user automatically.”
The new system combines a camera with light source attached to the nut of the drive and an artificial intelligence (AI) that evaluates the image data. As the nut moves on the spindle, it takes individual pictures of each spindle section, enabling the analysis of the entire spindle surface.
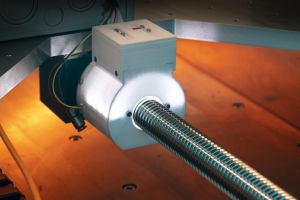
Artificial intelligence for mechanical engineering
Combining image data from ongoing operations with machine-learning methods enables system users to assess directly the condition of the spindle surface. “We trained our algorithm with thousands of images so that it can now confidently distinguish between spindles with defects and those without,” says Tobias Schlagenhauf (wbk), who helped development the system. “By further evaluating the image data, we can precisely qualify and interpret wear and thus distinguish if discoloration is simply dirt or harmful pitting.” When training the AI, the team took account of all conceivable forms of visible degeneration and validated the algorithm’s functionality with new image data that the model had never seen before. The algorithm is suitable for all applications that identify image-based defects on the spindle surface and is transferrable to other applications.
Being “The Research University in the Helmholtz Association”, KIT creates and imparts knowledge for the society and the environment. It is the objective to make significant contributions to the global challenges in the fields of energy, mobility, and information. For this, about 10,000 employees cooperate in a broad range of disciplines in natural sciences, engineering sciences, economics, and the humanities and social sciences. KIT prepares its 22,800 students for responsible tasks in society, industry, and science by offering research-based study programs. Innovation efforts at KIT build a bridge between important scientific findings and their application for the benefit of society, economic prosperity, and the preservation of our natural basis of life. KIT is one of the German universities of excellence.